Introduction to Inductive Proximity Sensors
In an age where automation and precision control are paramount, inductive proximity sensors stand out as critical components in modern technology. So, what is an inductive proximity sensor exactly? It’s a device equipped to detect the presence of metallic objects without any physical contact, making it invaluable in a vast array of applications. Fundamentally, an inductive proximity sensor works by generating an electromagnetic field and then scrutinizing any disturbances caused by a metallic object entering this field. It’s this non-contact detection capability that underscores their role in sectors like automation, manufacturing, and robotics.
The Basics of Inductive Proximity Sensors
An inductive proximity sensor typically consists of several key components: a coil, an oscillator, a proximity detector circuit, and an output interface. Its core function is to emit an electromagnetic field through the coil, which then operates as the detecting medium. When a metal object comes into the proximity of this field, the internal oscillator is affected, leading to changes in the field’s properties. These changes are picked up by the sensor’s circuitry, triggering a switch in the output signal to indicate the presence of the object.
Types of Inductive Proximity Sensors
Inductive sensors can be employed in countless applications, and with the rise of DIY electronics and hobbyists, the arduino inductive proximity sensor has gained popularity. This integration exemplifies how versatile these sensors are, being used in both industrial settings and within the maker community. The two primary types of inductive proximity sensors are:
- Shielded (Flush): Designed for installation flush within a metal surface; their sensing field is directed outwards from the sensor’s face.
- Unshielded (Non-Flush): These can be positioned without the need for a flush surface and typically sport a greater sensing range, although they may need more clearance to avoid unintended activation.
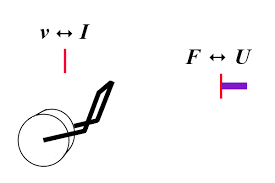
The Science Behind Inductive Proximity Sensors
The operation of inductive proximity sensors is grounded in their capability to generate an oscillating electromagnetic field. This field is typically created by an oscillator circuit—more specifically, a proximity detector circuit—that continually drives current through the sensor’s inductive coil. This field extends into the space around the sensor, and when a metallic object enters it, the field induces eddy currents within the object, altering field properties.
Oscillator Circuits Explained
The oscillator circuit within an inductive proximity sensor is a dynamic electronic system designed to consistently convert direct current (DC) into an alternating current (AC), which in turn generates the electromagnetic field around the coil. Metal presence distorts the steady generation of this field and leads to changes in the amplitude and frequency of the circuit oscillation, which the sensor is precisely calibrated to detect.
Applications of Inductive Proximity Sensors
Inductive proximity sensors have managed to insert themselves into numerous industries due to their steadfast detection capabilities. Notable applications include:
- Automation Systems: These sensors detect parts and components’ positioning along production lines, bolstering efficiency and preventing errors.
- Robotics: In conjunction with systems like Arduino, inductive proximity sensors facilitate the navigation and task execution of robots by ensuring accurate surroundings and object detection.
- Vehicle Detection: Employed to signal the presence of vehicles at traffic signals or in parking infrastructures, they serve as a reliable detection medium.
Industrial Automation and Robotics
Inductive proximity sensors’ impact on industrial automation is integral. They promote efficiency and reliability in automated systems by consistently providing exact detection capabilities. These sensors take center stage in tasks such as ensuring robotic arms execute precision welds by identifying metal components’ presence before initiating the welding sequence.
Improving Safety and Efficiency in Manufacturing
The implementation of inductive proximity sensors in the manufacturing sector has notably improved both safety and operational efficiency. These sensors eliminate the need for direct contact with parts, which reduces wear and tear on machinery and minimizes the risk of injury to human operators. Owing to their accurate detection capabilities, they can identify the precise position of a component, ensuring machines only operate when it is safe to do so, thereby avoiding potential accidents. Their use in harsh environments, where they can withstand high temperatures, dust, and moisture, exemplifies their adaptability and their contribution to maintaining consistent quality control standards.
Aspect | Description |
---|---|
Principle | Inductive proximity sensors detect metallic objects without physical contact by generating an electromagnetic field. |
Operation | When a metallic object enters the sensor’s electromagnetic field, it induces currents in the sensor, leading to a change in output. |
Applications | These sensors are widely used in manufacturing for object detection, position sensing, and automation. |
Advantages | Inductive proximity sensors offer high reliability, long service life, and resistance to environmental factors such as dirt and oil. |
Limitations | They are limited to detecting metallic objects and have a limited sensing range. |
Improvements | Ongoing advancements in sensor technology are extending sensing ranges and improving accuracy and integration with manufacturing systems. |
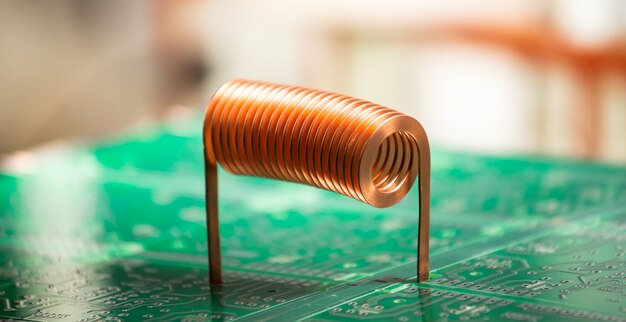
Installation and Usage Tips
To maximize the benefits of inductive proximity sensors, the installation process should be carried out with care, considering the specifics of each application. Here are some key tips to ensure proper installation and usage:
- Avoid Mounting Near Metal: Unless using shielded sensors, ensure there is sufficient clearance from metal objects to prevent false triggering.
- Mind the Sensing Range: Both shielded and unshielded sensors have specified sensing ranges. Place them within this range relative to the target object for optimal performance.
Calibration and sensitivity adjustments play a crucial role in sensor performance. Setting up the correct sensitivity ensures that sensors can detect the intended metallic object while disregarding incidental metal fragments or environmental interference. Ultimately, regular testing and maintenance are imperative to ensure that sensors continue to operate at peak efficiency over time.
Calibration and Sensitivity Adjustments
Calibrating an inductive proximity sensor is critical for its accurate function, as it fine-tunes the sensor’s detection capabilities to the specific operational environment. Sensitivity adjustment ensures the sensor responds appropriately to the presence of a target object, mitigating issues such as false positives or missed detections. Conducting periodic calibrations helps maintain the sensor’s precision, especially in facilities with changing conditions or where the introduction of new equipment might cause disturbances.
Challenges and Troubleshooting
Inductive proximity sensors are generally reliable, yet they still face challenges and can sometimes require troubleshooting. Common issues include:
- Interference: Strong electromagnetic fields from nearby equipment can interfere with sensor operation.
- Dirt and Debris: Accumulation can block the sensor’s face, preventing accurate detection.
- Wear and Damage: Over time, sensors can degrade, especially in harsh industrial environments.
In such events, it’s essential to systematically diagnose the problem by reviewing the installation environment, checking for physical obstructions, and testing the sensor’s functionality with known targets. If issues persist, consulting the manufacturer’s guidelines or seeking technical support may be necessary.
Dealing with Interference and False Readings
Minimizing interference and false readings is essential for maintaining operational efficiency. Strategies to achieve this include:
- Maintaining Proper Installation: Ensure sensors are installed according to manufacturer specifications with particular attention to spacing and alignment.
- Shielding and Wiring: Use appropriate shielding for cables and consider twisted-pair wiring to reduce electromagnetic interference from other equipment.
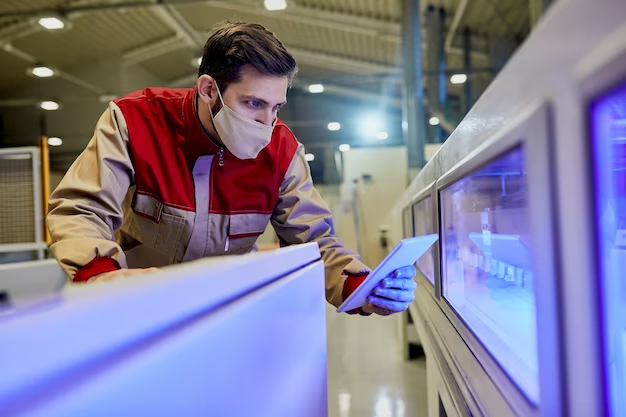
Conclusion
Inductive proximity sensors are a cornerstone technology in the realm of automation and manufacturing. Their ability to detect metallic objects accurately and reliably without contact has revolutionized the efficiency and safety of numerous processes. With proper installation, calibration, and maintenance, these sensors deliver consistent performance and durability, even in the most challenging industrial environments. By understanding how inductive proximity sensors work, industries can continue to harness their capabilities to foster innovation and streamline operations.
FAQs After Conclusion
- Can inductive proximity sensors detect non-metallic objects? No, inductive proximity sensors are designed to specifically detect metallic objects. Non-metallic objects do not induce enough change in the sensor’s electromagnetic field to be detected.
- How can I test if my inductive proximity sensor is working correctly? You can test an inductive proximity sensor by bringing a metal object within its sensing range and observing the output signal. This should change state if the sensor is operating accurately.
- What should I do if my sensor is giving false readings? If you receive false readings, check for nearby sources of electromagnetic interference, verify the sensor’s installation, and adjust the sensitivity settings. If problems persist, consult the manufacturer’s troubleshooting guide.
- Are inductive proximity sensors affected by environmental conditions? While they are quite robust, extreme temperatures, moisture, dust, and corrosive substances can affect sensor performance. Using sensors with the appropriate environmental rating for your specific application is crucial.
- Can inductive proximity sensors be used in outdoor settings? Yes, inductive proximity sensors can be used outdoors, but it’s important to select sensors with proper environmental sealing to withstand weather conditions and any potential contaminants.